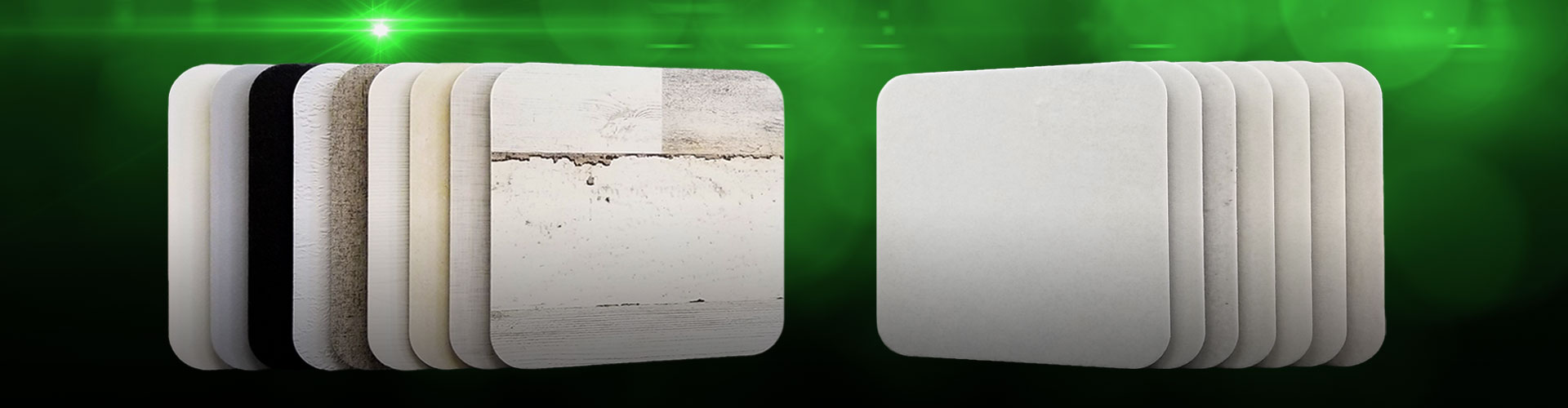
Azdel Onboard Composite
Interiors & Exteriors
Since 2006 Azdel Onboard® composite panels have been used regularly in place of plywood for RV wall construction. Made of a patented blend of fiberglass and polypropylene, our composite sheets help create technologically superior walls that will extend the life of your RV.
RVX (Standard)
RVX composite is our standard substrate for general lamination of most RV applications, such as sidewall interiors and exteriors, front and rear walls, slide-outs, roofs, ceilings, floors and more. The benefits are extensive, as you will learn during your time on this site. It forms excellent mechanical bonds with adhesives made for porous surfaces and allows for lamination with a wide range of materials. It can be lofted or compressed and thus is quite versatile. As such, it can be and is used in other construction such as lavatory and cargo trailers, buses and cube vans, modular and mobile structures, ceiling panels, office walls and partitions, and heavy truck inserts and interior wall panels. Its close relative, SuperLite™, is used for custom-molded parts in a variety of locations in cars and trucks seen on the road every day.
One slight deviation from RVX is RVZ. RVZ has a slightly different proportion of fiberglass and polypropylene, and is a denser sheet than those designated as RVX. This is currently only available in a 4.7mm sheet. The increased density provides a bump in both stiffness and impact resistance, and makes for an incredible substrate in a variety of applications. It is the primary replacement for larger units that used double layers of lauan in their walls.
The touchable surface of our material is a scrim, a thin fabric over our core that provides a smoother, more uniform finish, while allowing glue to penetrate easily to achieve a superior mechanical bond. Typically there is a white and a black scrim on opposing sides of our sheets, but they perform the same.
Thicknesses that see regular production and are stocked by most distributors include 2.7, 3.6, 4.7 and 5.2 (millimeters). Others are available for order.
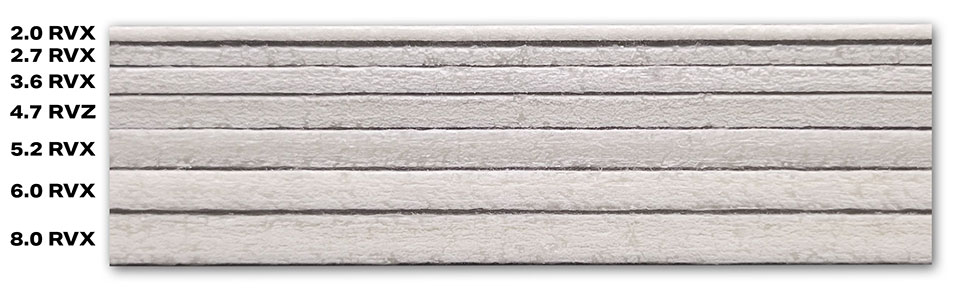
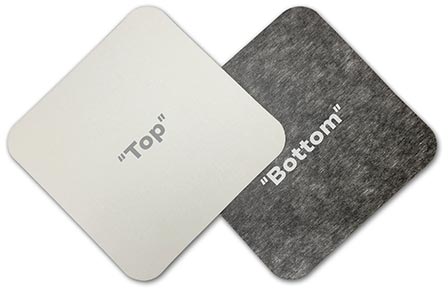
RVX-R / EcoLite™
A lesser known version in our composite family, but equally effective, is our RVXR, or more commonly referred to as EcoLite. In a green approach to resource utilization, unused, ground-up material is reintroduced to the production line to blend perfectly with the virgin pulp, producing an alternative material with properties nearly identical to those of RVX, with a couple exceptions.
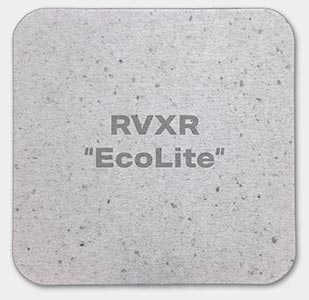
Aesthetically, RVXR displays traces of its material blending while remaining exactly the same to the touch. But one added benefit is its enhanced flexibility. Flex testing has shown RVXR/EcoLite is the best equipped material in our portfolio to handle the stresses of tighter radius applications. Learn more about our flex testing!
FRXA
Different industries have specific standards for their common construction materials. Some of those standards refer to a material’s ability to withstand heat or even fire. Materials used in the making of a vehicle’s interior or the walls of an office must have some minimum resistance to fire, if not be self-extinguishing. Such is the case with many other construction standards. As such, the development of our FRXA composite has opened the door to additional industries that have strict minimum requirements for flame resistance. While the standard for RV interiors is merely ASTM E-84 Class C, and our RVX and RVXR materials are a step better at Class B, our FRXA version is formulated to achieve a Class A rating, suitable for many applications. The appearance of FRXA sheets is virtually identical to that of the better known RVX.
Learn more about common FR standards and flame and burn resistance testing.
Interior Options for Azdel Composite
More manufacturers are accepting that Azdel Onboard composite sheets can be used as their interior substrate. They may simply have a distributor laminate a stock vinyl décor layer to our material, or a manufacturer could opt for one of our in-house options called DuraBlend™. All of our DuraBlend interiors are made by introducing a décor film to our core during the production process. The layers naturally bond together to form a new, durable interior panel option that reduces weight on an RV. Additionally, the separate step of lamination by distributors is eliminated, saving time, labor, adhesives and cost. We consider this an “inline” product.
The inline process described above is also used for our more basic finishes for less decorative areas. We use a polypropylene (PP) film on our composite, which becomes an excellent waterproof option for accent areas, storage areas, shower surrounds and more. The finish has a very light and subtle texture. We currently offer gray, white and black in this film, but many more colors are available by special order. The black option is also used as the underside to many of our suggested floor configurations.
Interior options exist for sidewalls, ceilings, cargo areas, shower surrounds and more. And that’s just for RV’s! Browse our various applications through the menu above for more ideas. You might also check out our Interior Wall Décor Panels page. Any of the above material grades can be used to make any of the interior panels described here. Learn more about the surface testing of our in-line interiors.
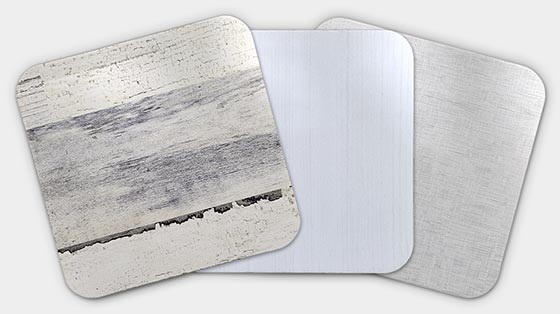
Samples of DuraBlend Interior Décor
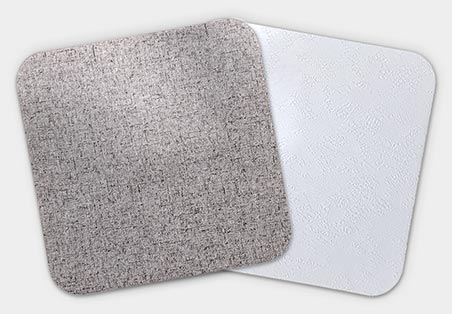
Samples of Distributor Vinyls: Wall & Ceiling
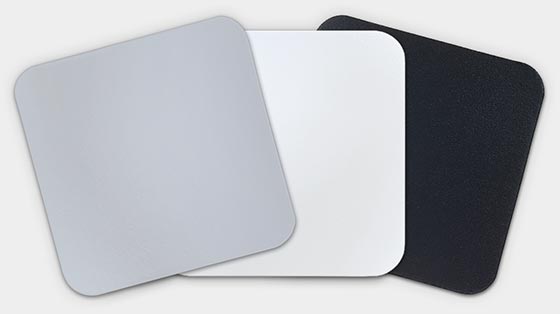
Our waterproof inline PP Film options