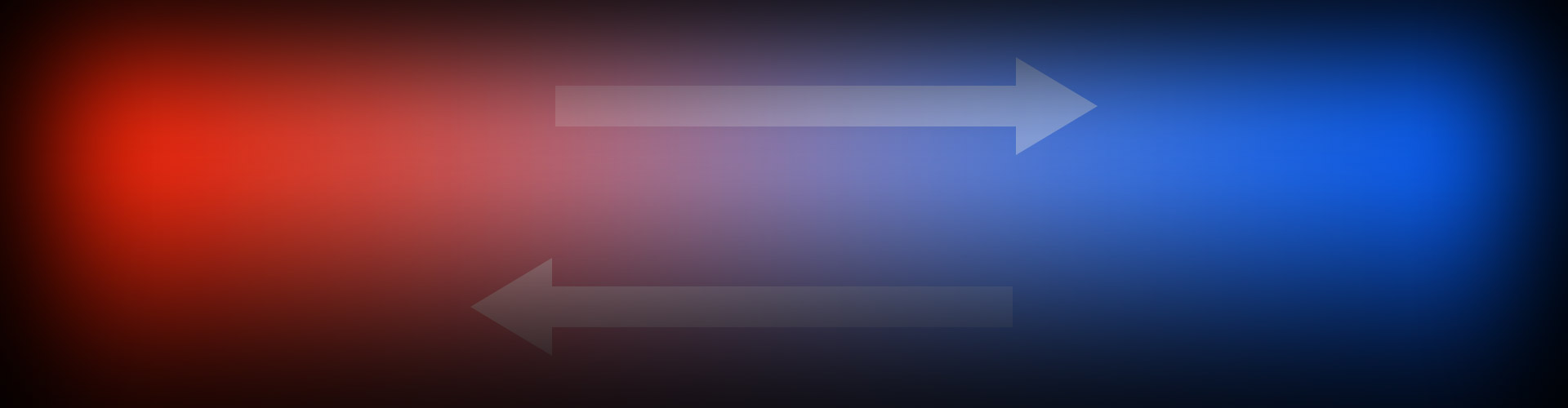
Thermal Transmission Resistance
& R-Value
We are often asked what the R-Value is of Azdel Onboard® composite. In the past we estimated. We were wrong. It’s better!
What is R-Value?
In simple terms, R-Value is a measure of resistance to heat flow through a barrier. The barrier could be a single layer of material like an insulation batt, or multiple layers of construction material in a structured wall. The higher the value, the more resistance to heat flow a material offers, and the better insulated your unit will be. The R-value standard of thickness is one inch of material so, generally, when a figure for R-value is provided, it is assumed to be based on the standard one-inch thickness. Adding more than an inch of that material will increase the actual insulation value, and vice versa.
Thermal Transmission Resistance of Azdel Composite
Below are depictions of the transmission of hot and cold air through different layers: Azdel composite and wood. Each layers appears as a frame to better illustrate the flow of hot and cold air. You will notice, however, that the amount passing through the Azdel composite is reduced from that of the wood sample. This is what the tests revealed, and this is what would happen in real world conditions. So then, what is the R-value of Azdel composite?
Thermal Transmission: Azdel Composite
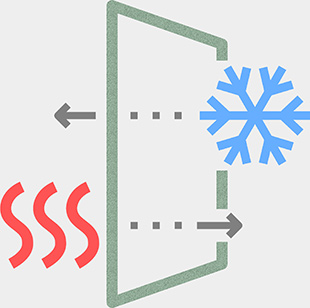
R-value = 4.65 @ 980gsm
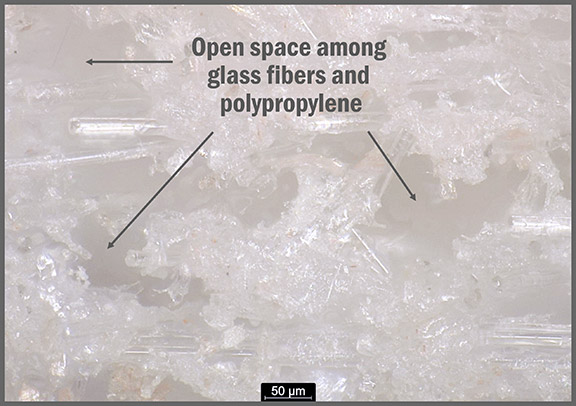
Image of Azdel composite under microscope, magnified 1,050 times.
Thermal Transmission: Lauan/Plywood
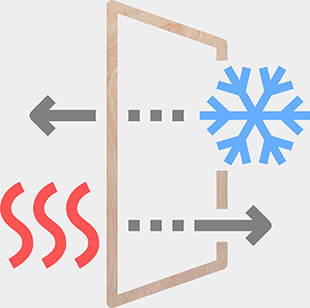
R-value = 1.0-1.2
The R-value of Azdel Onboard composite was tested to be 4.65 at a material weight of 980gsm. Typical plywood is known have an R-value of 1.0-1.2. Thus, Azdel was proven to be several times better, and even better than we previously estimated. But why?
Think of traditional fiberglass insulation batts. They are lightweight for their size, and they are porous — very porous. There is a lot of space between the fibers, and that space — the air between the fibers — serves as a virtual insulator from new air trying to pass through it. This is why our porous material performed so well.
The image above is our core magnified 1,050 times. The space between the fibers and other substances is clearly visible. You might consider these insulation pockets. This concept is not unlike the reason why our composite has such good sound absorption.
Not All Composites Are Created Equal
If there is one thing that southern states have in common, it’s that it gets very hot during the summer across all of them. It is not uncommon for the exterior of an RV to get to, or exceed, 120°F. It might reach that temperature for several consecutive days or weeks and, for darker surfaces that absorb more heat, it can get even hotter. Many RVers reside or vacation in those regions, and they understand very well the heat that their vehicles and RVs must endure. We wanted to as well.
We continually subject our composites to various tests to ensure they are able to withstand the rigors of road travel, harsh weather, extreme temperatures, and time. Some tests are outsourced to accredited labs, while others are done in house. Among those we conduct is the Sun Load test.
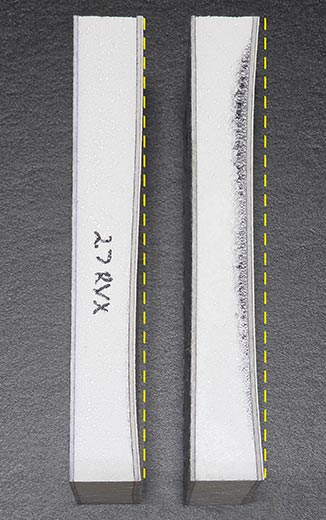
Left – Azdel Right – Alternative
The Sun Load test is an accelerated test to simulate the effects of prolonged exposure to hotter air and sunlight. We focus an infra-red lamp on the center of the exterior wall of each sample, maintaining 100°C (212°F) for eight hours, then off for 16 hours. We repeat this cycle to run a total of five times.
The sidewall samples are constructed similarly with the exception of the composites. In both images, the Azdel sample is on the left side. The other sample is made with an alternative composite behind the FRP (outer fiberglass) which is facing to the right.
The samples were cut in half to reveal the center cross-section of each piece where the heat was expected to do the most damage. It’s those areas that are shown here.
By way of melting and/or shrinkage, all samples experienced heat damage to the foam through the outer skin. However, the Azdel samples held up much better in the extreme heat compared to the alternate samples, which were left with large cavities in the wall while warping the skins significantly more. This was done with multiple samples, all with similar results.
We already knew that Azdel was about four times better than lauan/plywood for insulation. But this left us with no doubt that Azdel Onboard composite is the superior choice even compared to other composites when it comes to insulating from heat exposure.
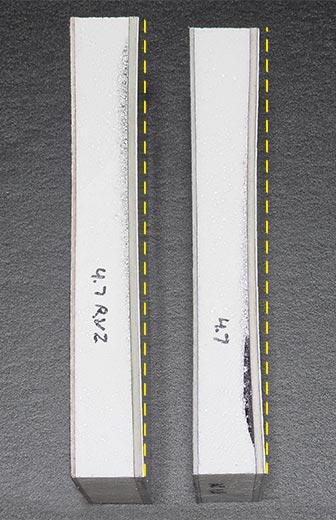
Left – Azdel Right – Alternative